Quality control achieved with the laboratory balance
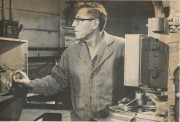
Laboratory balances can be quality control tools on the production floor. In the manufacture of cemented carbide tools, cutting tool materials and wear parts, balances are located at the presses that form green carbide compacts from powder, for accurate check of the weight of powder-feed to the dies. They are used during press setup, and for periodic checks during production runs, at each cold-forming press.
To insure proper density after sintering, a major factor in carbide quality, the proper weight of powder must be contained within the volume fixed by as-pressed dimensions. Length and width are fixed by accurate die sets. Height is fixed by adjustment of press stroke, checked by micrometer. Weight is fixed by adjustment of the powder feed mechanism.
If weight adjustment could not be checked at the press, the operator would have to shut down his press and go to a balance for checking. The setup often requires 4 to 6 trials, before feed-weight is adjusted within the extremely close limits required by VR/Wesson quality control. Also checks are made frequently during runs. The time savings is substantial.
The carbide products involved are in the 2 to 70 grams weight range with some up to 500 grams. Then there are some parts as small as 0.6 grams which are weighed a few at a time.
These particular balances, are made by The Torsion Balance Company. And an optical check-weigher is centrally located, and used as a master against which all other balances are compared.
I remember, very well, how disturbingly delicate our laboratory balances were in college chemistry, but then they were not dial operated either—the tweezers and the strip weights bit. These shown here must be really rugged to withstand shop abuse by operator, shop vibration and carbide dust. I understand this type of balance dispenses with the knife edge principle, in favor of flexing torsion bands. No doubt this is one of the reasons for accuracy and long life.
Published in 1968